スプリングの性能について
スプリングの性能
スプリングの性能は、その設計はもちろんですが、材料の性能が製品となったときにその強度・耐久性・靭性・疲労強度などにそのまま大きく影響します。
たとえ、最良の設計でスプリングを製作したとしても、使用する材料が悪くてはその性能は発揮できません。そのスプリングの材料となるオイルテンパー線も、現在のところ国内で生産しているのは数社しかありません。材料メーカー各社はともにその使用目的にあわせて独自の技術で製品に特長づけを行っています。
|
素材
スプリングの素材はもちろん鉄です。
ただ単に鉄といっても、普通鋼(SS材等)、特殊鋼(合金など)、特殊用途鋼(ステンレス鋼・ばね鋼)の3種類に分けることができます。
厳密に言えばその種類の中でも、一つ一つはかなり細かく細分化されていますが、
ここでは特殊用途鋼の中に属する『ばね鋼』について取り上げます。
ばね鋼と一言でいっても、中にはピアノ線やギター弦から始まり、かなりの広い範囲に及びます。もちろんそれぞれの性能や性質は同じばね鋼でもかなり変わってきます。
基本的なばね鋼の規格は、国内ではJIS G3560で制定され、海外ではISOおよびDIN、SAE等にそれぞれ準ずる規格が制定されていて、それぞれに規格化された製品が存在します。たとえば、一般的にばね鋼をあらわすSUP9/10/12やSAE9254(SAE規格)という名称のばね鋼もそれぞれの規格に沿った製品の名称ということになります。
それらの鋼材を主体として、各社が独自に特殊元素を添加した材料が、現在市場で生産および販売されている自動車用コイルスプリングの素材として使用されています。
|
熱処理
厳格に管理された最高の材料を使用しても、その材料の性能をフルに引き出すためには徹底した熱に関する処理が重要になってきます。
たとえばコイルスプリング用シリコンクロムオイルテンパー線は、初期の焼入れ状態で835HVまで硬度が上がります。この数値はビッカース硬さという基準で計測された数値ですが、この基準数値の範囲は160〜940HVであることからみて、かなりの硬度まで上がることになります。ですが、硬度が上がれば強度があるように錯覚しますが、硬度がある反面、耐衝撃性については非常にもろくなっており、残念ながらこのままでは使用できません。そのため、焼きなまし(ブルーイング)という徹底管理されたもとでおこなう低温熱処理をすることにより、硬度を530HVくらいまで落とす必要があります。
この時点で引っ張り強度に換算すると1820MPa(186kgf/mm2)という数値に落ち着きます。この状態でやっと自動車用スプリングとして使用できます。
では、なぜ熱処理をおこなうことにより硬度が上がるのでしょうか?
鉄に限らず物質は内部に結晶構造を持っています。その物質に対して熱を加えることにより、結晶構造を最適に変化させます。これを基本的な熱処理といいます。
まず、焼入れというのは炭素を含んだ材料にある温度まで熱を加え、急激に冷却することで非常に硬い結晶構造(マルテンサイト)を得ることができます。大概の鉄には炭素が多少なりとも含まれているため、通常鉄を焼入れすると硬くなるというのはこれに当てはまります。
物質に対して、その得ようとする特性に合わせて加温、冷却を適度におこなうことで内部構造を目的に合わせ変化させることを総称して熱処理といわれています。
『鉄は熱いうちに打て』ではないですが、鉄の性能を決定するのはこの熱処理であると言いきれます。どのような条件で熱を加え、それをいかに管理するかが品質を決定づける大きな要素であることはいうまでもありません。
|
成形方法による熱管理の違い
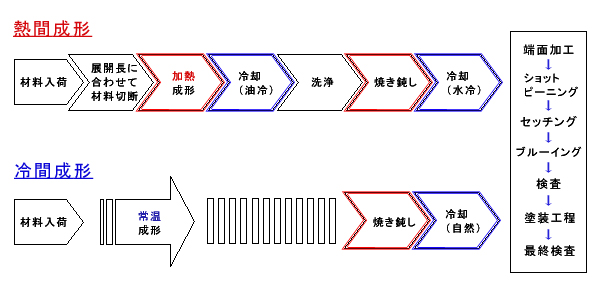
一番大きな違いは、上記に述べた重要となる熱処理を、どこで、どの工程で行うかということです。
冷間成形の場合、使用する材料はあらかじめ、適切で正確に制御された管理のもとに焼入れ処理がおこなわれた材料メーカーの設備で製作された材料を、そのまま使用します。ですから、材料入荷後、材料を機械にセットして成形工程を始めるときにはすでに完全な状態に焼入れ処理はおこなわれています。
成形後に焼きなまし(ブルーイング)の処理をおこなうだけですので熱処理が容易で、かつ安定した製品の生産が可能になります。
それに対して熱間成形の場合は、材料を成形(コイリング)する際に熱を加えるという作業が付帯します。もちろん成形後にも熱処理があります。これには、厳密な熱処理の管理が必要であり、相応の設備が求められます。その2回の熱管理が不安定であった場合、その製品もそのまま不安定でバラツキが出ます。それほどに熱に関する管理は重要になり、設備も大掛かりなものになります。
(上記は一般的な成形工程の違いを説明しています。
耐疲労性・強度を必要とする条件のスプリングについては、この限りではありません)
|
長年にわたり自動車用サスペンションを基盤として、
車高調やレース用ダンパーに使用される圧縮スプリング(直巻スプリング)やノーマル形状ローダウンスプリングをTPOに合わせて製作し続けてきました。
その蓄積されたデータとノウハウをスプリング製作会社の強力なサポートにより惜しげなくフィードバックできる環境が整い、敷居が高く思われていたワンオフ(オーダーメイド受注)に対応するための ブランドが完成いたしました!
バネレートは同じでも使用する線径と巻き数によってコイル間のピッチが変わり
復元スピードが違ってくるため、追従性や乗り心地も大きく違ってきます。
もちろんダンパーの減衰力の違いも大きな要因となりますが、『バネレートが同じならどのメーカーのスプリングも同じだろう』などと誤解されていることが多く、スプリングを変えるだけで違いが如実に現れることはなぜかあまり語られず、あまり知られていないのが現状です。
しかし、同一バネレート上に自由長(高さ)のバリエーションは数種類あっても、
自由長とバネレートを変えずにストローク量を変えるなど、量産されている製品においてはリクエスト不可能でした。
いわば、ユーザーに細かい選択の余地はなくスプリングメーカーが指定した仕様(言葉を悪く言えば、『吊るし』)のスプリングをバネレートと自由長の一覧表の中からどの車両においても共通で使うか、製造メーカー自体を変えることぐらいしかできませんでした。
ZEROスプリングはそういった固定概念をなくし、弊社でラインナップした仕様のほかにも、内径(または外径)を1ミリ変更することや、バネレートと自由長は同じでもストロークは違う仕様にするなど、ユーザーからの希望を直接取り入れた完全なオリジナル仕様で製作することも可能です。
◎ZEROスプリングはご要望に合わせて設計されたそれぞれの仕様に基づいて最適な成形方法を選択し、材料選定から徹底管理された製造工程を経て、常にクオリティーの高い製品づくりを行っております。
Copyright (C) SLASH. All Rights Reserved.
|